Цемент, песок, щебень, добавки
1. Цемент.
1.1. Портландцемент. Минералогический состав.
Для приготовления бетона в строительных
конструкциях наиболее широко используют неорганические вяжущие вещества. Эти
вещества при смешивании с водой под влиянием внутренних физикохимических процессов
способны схватываться (переходить из жидкого или тестообразного состояния в камневидное)
и твердеть (постепенно увеличивать свою прочность). Наиболее широкое применение
в производстве бетона получил портландцемент. Портландцемент – гидравлическое
вяжущее вещество, твердеющее в воде или на воздухе. Он представляет собой
порошок серого цвета, получаемый тонким помолом клинкера с добавкой гипса. Клинкер
– обожженная до спекания смесь, в которой преобладают силикаты кальция. Для получения
цемента высокого качества необходимо, чтобы его химический состав, а, следовательно,
и состав сырьевой смеси были устойчивы. При помоле к цементному клинкеру можно
добавлять до 20 % гранулированных доменных шлаков или активных минеральных добавок.
В результате обжига при 1450 _С образуются следующие
основные клинкерные минералы:
- Алит, трехкальциевый силикат – состава 3CaO*SiO2 или C3S . Основной минерал, оказывающий влияние на качество цемента. Алит обладает свойствами быстротвердеющего гидравлического вещества высокой прочности. Цементы высоких марок и быстротвердеющие цементы изготавливают с повышенным содержанием трехкальциевого силиката. Содержание в цементе – 3760%.
- Белит, двухкальциевый силикат – состава 2СаО*SiO2 или C2S. Медленнотвердеющее гидравлическое вяжущее средней прочности. Цементы с повышенным содержанием белита медленно твердеют, однако прочность их нарастает в течение длительного времени и в возрасте нескольких лет может оказаться достаточно высокой. Содержание в цементе – 15-37%.
- Трехкальциевый алюминат – состава 3СаО*Al2O 3 или С3А. Минерал-плавень, главная задача которого понижение температуры спекания сырьевой смеси. Твердеет быстро, но имеет низкую прочность. Содержание в цементе – 5-15%.
- Четырехкальциевый алюмоферрит – состава 4CaO*Al2O3*Fe2O3 или С4AF. Минерал-плавень. Твердеет быстрее силикатов, но медленнее алюмината. Содержание в цементе – 10-18%.
1.2. Прочность. Активность. Марка.
Основным свойством, характеризующим качество любого цемента, является его прочность (марка).
Марка цемента определяется испытанием стандартных образцов -балочек размером
4*4*16 см, приготовленных из раствора цемента и стандартного вольского песка,
с последующим твердением в течение 28 суток во влажных условиях. Испытания проводятся
на изгиб и сжатие. Прочность контрольных образцов на сжатие, выраженная в кгс/см2, является
маркой цемента. В строительстве применяют цементы марок 300, 400, 500, 550,
600. Действительную прочность цемента называют его активностью. Т.е. если контрольные
образцы показали прочность при сжатии 44 МПа, то активность этого цемента будет
44 МПа (≈ 440 кгс/см2), а марка – 400. При проектировании состава бетона
лучше использовать активность цемента, так как это обеспечивает более точные результаты
и экономию цемента. Помимо прочности к цементам предъявляются и другие требования,
важными из которых являются нормальная густота и сроки схватывания.
1.3. Физико-механические свойства
цемента.
Нормальной густотой
называют то содержание воды (в %), которое необходимо добавить к цементу, чтобы
получить определенную консистенцию цементного теста. Обычно эта величина равна
22-27% и увеличивается при введении в цемент при помоле тонкомолотых добавок,
обладающих большой водопотребностью (трепел, опока и др.). Нормальная густота
в известной мере определяет реологические свойства цементного теста и тем самым
влияет на подвижность бетонной смеси. Чем меньше нормальная густота цемента,
тем меньше водопотребность бетонной смеси, необходимая для достижения определенной
подвижности (жесткости) смеси. Сокращение расхода воды, в свою очередь, приводит
к уменьшению расхода цемента (при заданном В/Ц). В бетонах желательно применять
цементы с пониженной нормальной густотой. Сроки схватывания цемента, определяемые
на специальном приборе по глубине проникания иглы в цементное тесто, характеризуют
начало и конец процесса превращения материала в твердое тело. По стандарту требуется,
чтобы начало схватывания при температуре 20_С наступало не ранее, чем через 45 мин,
а конец завершался не позднее 10 ч. с момента затворения цемента водой. На практике
начало схватывания наступает через 1-2 ч, а конец – через 5-8 ч. Эти сроки обеспечивают
производство бетонных работ, т.к. дают возможность транспортировать и укладывать бетонные смеси и растворы до их схватывания. Сроки
схватывания можно регулировать путем добавления в бетонную смесь при ее приготовлении
различных химических добавок. Портландцемент имеет, как правило, тонкий помол:
через сито N008 (около 4900 отверстий на 1 кв.см. с размером ячеек в свету
0.08*0.08 мм) должно проходить не менее 85 % общей массы цемента. Средний размер
частиц цемента составляет 15-20 мкм. Истинная плотность портландцемента без добавки
составляет 3,05-3,15 г/см3. Плотность портландцемента при расчете
состава бетона условно принимают в уплотненном состоянии 1,3 кг/м3. Схватывание и твердение цемента –
экзотермические процессы. Практически 1 кг цемента М400 выделяет в бетоне за
7 суток с момента затворения цемента водой не менее 210 кДж. Для цемента М500
эта цифра составляет порядка 250 кДж. Тепловыделение зависит от минералогического
состава цементного клинкера, типа введенных добавок и тонкости помола. Из клинкерных
минералов наибольшим тепловыделением обладают трехкальциевый алюминат и трехкальциевый
силикат. Основное тепло выделяется в течение первых 3-7 суток твердения цемента.
Перевозят и хранят цемент так, чтобы предохранить его от увлажнения, распыления
и других потерь. Обычный цемент при нормальных условиях хранения через 3 мес.
теряет 20% прочности, через 6 мес – 30%, через год –40%. При использовании в производстве
лежалого цемента время перемешивания бетонной смеси увеличивают в 2-4 раза, вводят
добавки-ускорители твердения или применяют активацию цемента.
1.4. Виды цемента.
Основу большинства цементов составляет
портландцементный клинкер. Нормируя его минералогический состав и вводя минеральные
или органические добавки, получают различные цементы, несколько отличающиеся по
свойствам и применяемые в разных областях строительства.
- Бездобавочным портландцементом (ПЦ) называют цемент, не содержащий в своем составе минеральных добавок, кроме гипса. Обозначение по ГОСТ 10178-85 -ПЦ-500-Д0, где ПЦ – портландцемент. 500 – марка цемента. Д0 – добавок 0% (бездобавочный).
- Портландцемент с минеральными добавками. Содержит в своем составе до 20% гранулированного доменного шлака, до 10% природных активных минеральных добавок (трепела, опоки и др.), до 15% прочих активных минеральных добавок. Обозначения по ГОСТ 10178-85 -ПЦ-500-Д5 или ПЦ-500-Д20, где Д5(Д20) – максимальное содержание добавок в цементе.
- Шлакопортландцемент. Содержит в своем составе от 20 до 80% гранулированного доменного шлака. Отличается от ПЦ более медленным схватыванием (начало 4-6 ч, конец 10-12 ч) и твердением в первые 7-10 сут. При тепловлажностной обработке (ТВО) твердение шлакопортландцемента ускоряется в большей степени, чем у обычного ПЦ, что обусловливает его высокую эффективность в производстве сборного железобетона. Обозначение по ГОСТ 10178-85 -ШПЦ -400
- Быстротвердеющий портландцемент. Разновидность ПЦ с добавками. Через 3 сут твердения прочность на сжатие этого цемента не менее 25 МПа, марки 400, 500. Требования к минералогическому составу: С3S>50%, (C3S+C3A)>60%. Тонкость помола (удельная поверхность не менее 3500 см2/г).
- Сульфатостойкие портландцемент и шлакопортланцемент выпускают, нормируя минералогический состав, в котором ограничивается содержание менее стойких к сульфатной агрессии минералов. Этот цемент содержит до 50% С3S, 5% C3A, 10...22% (C3A+C4AF). Для получения сульфатостойкого портландцемента с добавкой при помоле к цементу добавляют до 20% гранулированного доменного шлака. Добавка связывает выделяющийся при гидратации С3А гидрат окиси кальция, что способствует повышению сульфатостойкости цемента, в этом случае содержание С3А ограничивают 8%. Сульфатостойкие цементы предназначены для бетонных и железобетонных конструкций, эксплуатируемых в условиях переменного уровня воды, а также сооружений, которые подвергаются агрессивному воздействию сульфатных вод при одновременном многократном замерзании и оттаивании или многократном увлажнении и высыхании. Завод-изготовитель гарантирует соответствие цемента требованиям ГОСТа в момент получения цемента, но не более чем через месяц после отгрузки. В паспорте помимо вида и марки цемента и названия завода-изготовителя указывается нормальная густота цементного теста и средняя активность цемента при пропаривании по режиму 2+3+6+4 ч, при температуре изотермического прогрева 85°С и испытании через сутки с момента изготовления.
Специальные виды цемента.
1)
Белый портландцемент
получают помолом маложелезистого отбеленного клинкера, приготовленного по специальной
технологии, предотвращающей его загрязнение, с необходимым количеством гипса
и небольшой добавкой диатомита. По степени белизны белый цемент подразделяют на
три сорта: высший, БЦ-1, БЦ-2. Коэффициенты яркости соответственно 80, 76, 72
%. За 100% принят коэффициент яркости сернокислого бария.
2) Цветные портландцементы получают совместным помолом белого клинкера, гипса и пигмента. Содержание минерального синтетического или природного пигмента не должно превышать 15%, а органического пигмента – 0,3% от массы цемента. Белый и цветные цементы предназначены для получения цветных бетонов, архитектурных деталей, облицовочных плит, проведения отделочных работ.
3) Напрягающий цемент получают совместным помолом портландцементного клинкера и напрягающего компонента, который включает в себя глиноземистый шлак или другие алюмосодержащие вещества, гипс и известь. Он обладает способностью значительно расширяться в объеме (до 4%) после достижения цементным камнем сравнительно большой прочности 15-20 МПа, что позволяет применять этот цемент для изготовления самонапряженного железобетона, в котором арматура получает предварительное напряжение вследствие расширения бетона. Напрягающий цемент и бетоны на его основе обладают высокими прочностью, водо и газонепроницаемостью. Его целесообразно применять для изготовления самонапряженных железобетонных труб, покрытий дорог и аэродромов, тоннелей и других подобных конструкций. При этом следует учитывать быстрое схватывание такого цемента (начало 2 мин, конец – 6 мин), а также необходимость применения специальных режимов твердения, обеспечивающих расширение цемента лишь после достижения бетоном прочности, необходимой для заанкеривания арматуры.
4) Расширяющиеся или безусадочные цементы применяют для приготовления водонепроницаемых бетонов. Особенностью этих цементов является наличие составляющих, увеличивающихся в объеме в результате физико-химических процессов, происходящих при твердении цемента.
5) Кислотоупорный цемент применяют для изготовления кислотостойких или жаростойких бетонов. Этот цемент состоит из тщательно перемешанного молотого кварцевого песка и кремнефтористого натрия, его затворяют на жидком стекле (Na2O(K2O)*nSiO2 ). Для получения необходимой консистенции жидкое стекло разбавляют водой.
2. Заполнители для бетона.
2.1. Основные характеристики.
Заполнители занимают
в бетоне до 80% объема и оказывают влияние на свойства бетона, его долговечность
и стоимость. Жесткий скелет из высокопрочного заполнителя несколько увеличивает
прочность и модуль деформации бетона, уменьшает деформации бетона под нагрузкой,
а также ползучесть бетона -необратимые деформации, возникающие при длительном
действии нагрузки. В специальных бетонах роль заполнителя очень высока, так как
его свойства во многом определяют специальные свойства этих бетонов. В бетоне
применяют крупный и мелкий заполнитель. Крупный заполнитель (более 5 мм) подразделяют
на гравий и щебень. Мелким заполнителем в бетоне является естественный или искусственный
песок. К заполнителям для бетона предъявляются требования, учитывающие особенности
влияния заполнителя на свойства бетона. Заполнитель является зернистым материалом,
для которого имеется ряд общих закономерностей. Наиболее существенное влияние
на свойства бетона оказывают зерновой состав, прочность и чистота заполнителя.
Зерновой состав показывает содержание в заполнителе зерен разной крупности. Он
определяется просеиванием пробы заполнителя через стандартные сита с величиной
отверстий от 0,14 до 70 мм и более. Различают рядовой заполнитель, содержащий
зерна различных размеров и фракционированный, когда зерна заполнителя разделены
на отдельные фракции, включающие зерна близких между собой размеров. Заполнитель
характеризуется наименьшей и наибольшей крупностью, под которыми понимают размеры
наименьших или наиболее крупных зерен заполнителя. На строительных объектах или
заводах сборного железобетона зерновой состав заполнителя подбирают, используя
реальные песок и щебень. Правильный выбор зернового состава заполнителя или соотношения
между песком и щебнем может быть сделан только с учетом состава бетона, в частности,
с учетом содержания цемента и воды. В бетонах высокой прочности с повышенными расходами цемента и в жестких бетонных смесях
долю песка или мелких фракций заполнителя в его общем объеме целесообразно несколько
уменьшать, исходя из конкретных свойств заполнителя и состава бетона. С зерновым
составом непосредственно связана пустотность заполнителя, определяемая возможностью
его плотной укладки. Зависимость пустотности от формы зерен заполнителя показана
на рис 1.
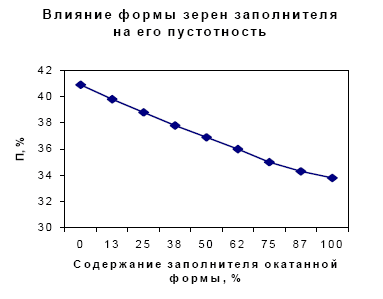
На пустотность оказывает заметное влияние содержание крупного и мелкого заполнителя (Рис. 2).
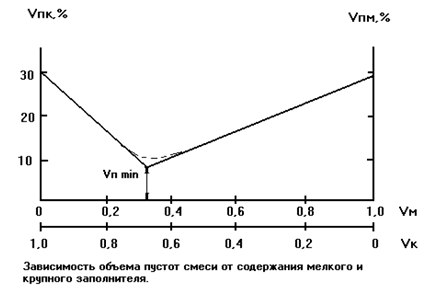
Пустотность в известной мере определяет расход цемента и другие свойства бетона. Пустотность заполнителей колеблется от 20 до 50 %. В бетоне желательно использовать заполнители, состоящие из нескольких фракций и имеющие наименьшую пустотность. Прочность заполнителя определяется не только прочностью горной породы, из которой он получен, но и крупностью зерен. При выветривании или дроблении породы разрушение происходит по более слабым местам структуры и прочность зерен как бы повышается. Естественные пески обладают прочностью при сжатии и растяжении, как правило, более высокой, чем прочность раствора или цементного камня. Прочность крупных заполнителей из прочных горных пород (гранита, диабаза и др.) превосходит по прочности раствор (Рис.3).
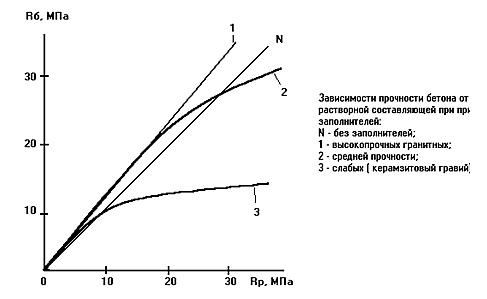
Прочность бетона на гранитном щебне несколько выше прочности раствора. При применении менее прочного крупного заполнителя прочность бетона при увеличении прочности раствора возрастает лишь до определенных значений, и дальнейшее повышение прочности раствора не приводит к повышению прочности бетона. Предельно достижимая прочность бетона тем ниже, чем меньше прочность крупного заполнителя, причем ее значение зависит также и от содержания заполнителя, постепенно увеличиваясь с уменьшением его количества. Большое влияние на прочность бетона оказывает чистота заполнителя. Пылевидные и особенно глинистые примеси создают на поверхности зерен заполнителя пленку, препятствующую сцеплению их с цементным камнем. В результате прочность бетона значительно понижается (иногда на 30-40 %). Корректировать отрицательное влияние грязного или некачественного заполнителя на свойство бетона путем повышения расхода цемента недопустимо.
2.2. Песок. Характеристики и свойства
Природный песок, применяемый для
производства обычного бетона, представляет собой образовавшуюся в результате
выветривания горных пород рыхлую смесь зерен (крупностью 0,14-5,00 мм) различных
минералов, входящих в состав изверженных (реже осадочных) горных пород. При отсутствии природного песка применяют песок, получаемый
путем дробления твердых горных пород. Песок для производства обычного бетона,
должен соответствовать требованиям ГОСТ 10286-80. Содержание в песке зерен, проходящих
через сито 0,14 мм, не должно превышать 10%, а содержание глинистых, илистых
и пылевидных примесей, определяемых отмучиванием – 3% по массе. Наиболее вредна
примесь глины, так как она, обволакивая зерна песка, препятствует сцеплению с
цементным камнем. От глинистых примесей песок очищают тщательной промывкой. Органические
примеси допускают только в очень незначительном количестве, т.к. они понижают
прочность и даже разрушают цемент. Крупность зерен определяют просеиванием песка
через стандартный набор сит с отверстиями в свету 5, 2.5, 1.25, 0.63, 0.315,
0.14 мм. Наличие в песке зерен крупнее 10 мм в песке не допускается, зерен размером
5-10 мм должно быть не более 5 % по массе. Остатки на каждом сите (в %), называемые
частными, характеризуют распределение зерен песка по степени крупности, т.е. зерновой
(гранулометрический) состав песка. Складывая частный остаток на данном сите с
суммой остатков на предыдущих ситах, определяют полные остатки (в %) на ситах.
Для условного выражения крупности песка пользуются модулем крупности,
обозначающим сумму полных остатков на ситах стандартного набора, деленную на
100:
М кр =∑ΔG полн /100
Модуль крупности позволяет оценивать влияние заполнителя на свойства бетонной смеси и бетона лишь приблизительно. Смеси с различным зерновым составом могут иметь одинаковый модуль крупности, но различные пустотность и удельную поверхность и соответственно по-разному влиять на подвижность и другие свойства бетонной смеси и бетона. Если песок крупный, то это еще не значит, что он вполне пригоден для бетона. Крупный песок может иметь большой объем пустот, который придется заполнять цементным тестом, что увеличивает себестоимость бетона. Для полной характеристики песка важна величина его пустотности. В доброкачественном песке она не должна превышать 38%. Для бетона наиболее пригоден крупный песок, содержащий достаточное количество средних и мелких зерен. При такой комбинации зерен объем пустот будет малым, а площадь их поверхности – небольшая. Плотность песка зависит от его истинной плотности, пустотности и влажности и определяется в сухом рыхлом состоянии. Для высококачественного бетона она должна быть не ниже 1550 кг/м3, а в остальных случаях не ниже 1400 кг/м3. Самый большой объем песок занимает при влажности около 5-7%, с повышением или понижением влажности объем песка уменьшается. Рекомендуемый состав песка представлен на рис. 4.
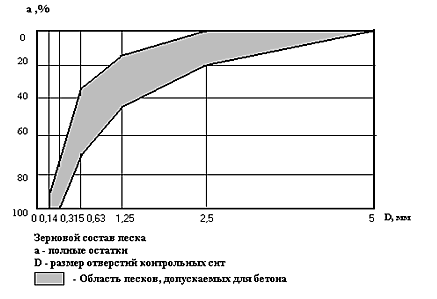
2.3. Гравий. Характеристики и свойства.
Гравием называют рыхлый материал, образовавшийся в результате естественного
разрушения (выветривания) горных пород. Гравий состоит из более или
менее окатанных зерен размером 3-70 мм. В нем могут содержаться зерна высокой
прочности (гранитные) и слабые зерна (пористых известняков). Обычно он содержит
примеси пыли, глины, иногда и органических веществ, а также песка. При большом
содержании песка такой материал называют песчаногравийной смесью. Для бетона
желательна малоокатанная форма зерен гравия, малопригодна окатанная, еще хуже
– пластичная или лещадная с шириной в три раза и более превышающей толщину (предельное
содержание в составе 15% по массе). Крупность гравия определяют просеиванием
его через стандартный набор сит с круглыми отверстиями размером 70, 40, 20,
10 и 5 (или 3) мм. При изготовлении бетона большое значение имеет максимально
допускаемая крупность гравия, определяемая размером отверстия сита, на котором
полный остаток не превышает 5% от общей навески. Для удобной укладки бетонной
смеси нельзя применять гравий крупнее ¼ минимального размера сечения конструкции
и больше минимального расстояния между стержнями арматуры в ж/б конструкции.
Для бетона желателен крупный гравий, но с достаточным содержанием средних и мелких
зерен. Пустотность гравия не должна превышать 45%. Прочность зерен гравия должна
обеспечивать получение бетона, прочность которого на 20-50% превышает заданную.
В гравии допускается не более 1% по массе глинистых, илистых, пылевидных примесей,
количество которых определяют отмучиванием. Если в гравии количество примесей
больше допустимого, то его промывают водой. В природе встречаются готовые смеси
песка и гравия. В этих случаях необходимо проверять постоянство состава и соответствие
песчаной и гравийной частей существующим стандартам. Чаще всего смеси по составу
непостоянны, и их приходится разделять на песок и 2-3 фракции гравия.
2.4. Щебень. Характеристики и свойства.
Щебнем называют материал, полученный
в результате дробления камней из горных пород.
Щебень имеет остроугольную форму.
Для приготовления бетона лучше использовать щебень, близкий по форме к кубу или
тетраэдру. Форма щебня зависит от структуры каменной породы и типа камнедробильной
машины. Для производства щебня используют гранит, диабаз и другие изверженные
породы, а также плотные осадочные породы – известняк, доломит и измененные породы
– кварцит. Наиболее широко в строительстве применяют известняковый и гранитный
щебень. К крупности, зерновому составу, прочности щебня предъявляют те же требования,
что и к гравию. Щебень чище гравия, обычно он не содержит органических примесей.
Предельное содержание глинистых и пылевидных примесей допускается: для бетонов
300 и выше – 1% в щебне из изверженных пород и 2% в щебне из карбонатных пород,
для бетонов более низких марок – соответственно 2 и 3% по массе. Для обычного
бетона можно применять щебень только из каменных пород. Необходимая прочность
исходной каменной породы в насыщенном водой состоянии Rщ >2R б для бетона 300
и выше Rщ>1,5Rб для бетонов более низких марок. Для бетона в конструкциях,
подвергающихся насыщению водой и замораживанию, желательно применять щебень водопоглощением
не более 3% по массе, а без замораживания – не более 5%. Рекомендуемый состав
гравия и щебня представлен на рис. 5.
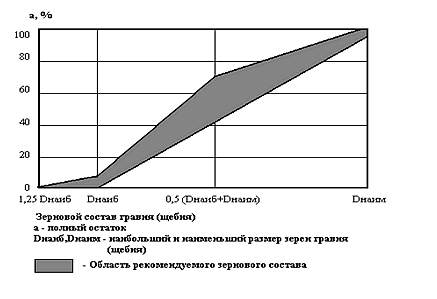
3. Добавки к бетонам.
Для регулирования свойств бетона, бетонной смеси и экономии
цемента применяют различные добавки. Их
подразделяют на 2 вида:
3.1. Химические добавки. Классификация.
Химические добавки вводятся в бетон
в небольшом количестве (0,1-2% от массы цемента) и изменяют в нужном направлении
свойства бетонной смеси. Их классифицируют по основному эффекту действия:
- Регулирующие свойства бетонных смесей – пластифицирующие (увеличивающие подвижность бетонной смеси), стабилизирующие (предупреждающие расслоение бетонной смеси), водоудерживающие.
- Регулирующие схватывание бетонной смеси и твердение бетона – ускоряющие или замедляющие схватывание, ускоряющие твердение, противоморозные.
- Регулирующие плотность и пористость бетонной смеси и бетона – газообразующие, воздухововлекающие, пенообразующие, уплотняющие, гидрофобизирующие; добавки – регуляторы деформаций бетона, расширяющие добавки.
- Повышающие защитные свойства бетона к стали – ингибиторы коррозии стали.
- Придающие бетонам специальные свойства – гидрофобизирующие, антикоррозионные, красящие, электропроводящие. Некоторые добавки обладают полифункциональным действием. В этом случае добавку классифицируют по наиболее выраженному эффекту действия. В последнее время разработаны новые химические добавки – суперпластификаторы. Эти добавки в большей степени увеличивают подвижность и текучесть бетонной смеси, существенно улучшают строительнотехнологические свойства бетона, могут обеспечить значительную экономию цемента. Суперпластификаторы (СП) – синтетические полимерные вещества, которые вводят в бетонную смесь в количестве 0,1-1,2% от массы цемента. СП не замедляют твердения бетона, так как адсорбционный слой добавки на поверхности зерен цемента проницаем для воды, а ее дефлокулирующее действие увеличивает поверхность контакта цемента и воды и число новообразований. Введение СП особенно эффективно для производства сборного железобетона, где увеличение скорости твердения бетона имеет важное значение, и где применение обычных пластификаторов проблематично. Большинство добавок растворимы в воде, и их вводят в бетоносмеситель в виде предварительно подготовленного раствора. Оптимальная дозировка зависит от вида цемента, состава бетонной смеси, технологии изготовления конструкции. Обычно применяют (в % от массы цемента) пластифицирующих добавок – 0,1-0,3; суперпластификаторов – 0,5-1; воздухововлекающих – 0,010,05; ускорителей твердения –1-2. На практике оптимальную дозировку определяют опытным путем.
3.2. Тонкомолотые добавки.
Тонкомолотые добавки вводят в бетон в количестве 5-20% и более от массы цемента. Эти добавки
предназначены для экономии цемента и для получения плотного бетона при малых расходах
цемента. К тонкомолотым добавкам относят золы, молотые шлаки, отходы камнедробления,
пески и некоторые другие материалы, позволяющие изменять в нужном направлении
свойства бетона, повышающие его плотность, водостойкость, жаростойкость и др.
При введении тонкомолотых добавок следует учитывать, что на цементных заводах
в цемент уже, как правило, введено определенное количество минеральных добавок.
Излишнее введение тонкомолотых добавок в бетон без проведения специальных мероприятий
по гомогенизации и активации бетонной смеси может снизить долговечность бетона.
При проектировании применения в бетоне добавок необходимо проводить технико-экономические
расчеты для прогнозирования ожидаемого эффекта.
4. Вода для приготовления бетонной смеси.
Для приготовления бетонной смеси используют водопроводную
питьевую, а также любую воду, имеющую водородный показатель рН не менее 4. Вода
не должна содержать сульфатов более 2700 мг/л (в пересчете на SO42-)
и всех солей не более 5000 мг/л. В сомнительных случаях пригодность воды для
приготовления бетонной смеси необходимо проверять путем сравнительных испытаний
образцов, изготовленных на данной воде и на обычной водопроводной. Для поливки
бетона следует применять воду такого же качества, как и для приготовления бетонной
смеси.
5. Проектирование состава тяжелого бетона.
5.1. Основные положения единой методики определения состава бетона.
В результате проектирования состава
бетона должно быть определено такое соотношение между материалами, при котором
будет гарантирована прочность бетона в конструкции с учетом технологии ее изготовления,
необходимая подвижность бетонной смеси и экономичность бетона (минимальный расход
цемента). Проектирование состава бетона включает:
- Назначение требований к бетону, исходя из вида и особенностей службы и изготовления конструкции.
- Выбор материалов для бетона и получение необходимых данных, характеризующих их свойства.
- Определение предварительного состава бетона.
- Проверку состава в пробных замесах.
- Контроль за бетонированием.
- Корректировкусостава в процессе производства при колебаниях свойств заполнителя и других факторов.
Определение предварительного состава бетона производят на основе зависимости прочности бетона от активности цемента, цементно-водного фактора, качества используемых материалов и зависимости подвижности бетонной смеси от расхода воды. Требования к прочности бетона указывают в рабочих чертежах. Подвижность (жесткость) бетонной смеси назначают в зависимости от размеров конструкции, густоты армирования, способов укладки и уплотнения (см. таблицу 1.).
Таблица 1.
Конструкции и способ уплотнения | Подвижность, см |
---|---|
1. Сборные железобетонные с немедленной распалубкой, формуемые на виброплощадках или с вибронасадкой | - |
2. Перекрытия с пустотами, стеновые панели, формуемые в горизонтальном положении на виброплощадках. | 1...4 |
3. Густоармированные элементы (колонны, ригели, плиты), изготовляемые с применением наружного или внутреннего вибрирования. | 5...9 |
4. Формуемые на ударно-вибрационных установках. | - |
5. Формуемые в кассетах. | 7...14 |
6. Центрифугированные. | 5...10 |
7. Гидропрессованные. | - |
При перекачивании бетонной смеси насосом осадка конуса должна быть 6-8 см. Бетонная смесь обладает необходимой удобоукладываемостью только при содержании в ней достаточного количества цемента. Минимальный расход цемента зависит от консистенции бетонной смеси и крупности заполнителя (см. табл. 2) .
Таблица 2.
Смесь | Минимальный расход цемента кг/3 при предельной крупности заполнителя, мм | |||
---|---|---|---|---|
10 | 20 | 40 | 70 | |
Особо жесткая (Ж=20с) | 160 | 150 | 140 | 130 |
Жесткая (Ж=10-20с) | 180 | 160 | 150 | 140 |
Малоподвижная (Ж=5-10с) | 200 | 180 | 160 | 150 |
Подвижная (ОК=1-10 см) | 220 | 200 | 180 | 160 |
Очень подвижная (ОК=10-16 см) | 240 | 220 | 210 | 180 |
Литая (ОК>16 см) | 250 | 230 | 200 | 190 |
Примечание: Ж -жесткость по стандартному вискозиметру ОК-осадка конуса |
Если при определении состава бетона окажется, что расход цемента, требуемый из условия получения заданной прочности, ниже указанных значений, то в расчет принимают минимальный расход цемента. Для экономного расходования цемента необходимо, чтобы его марка по возможности превышала требуемую прочность бетона:
Прочность бетона, МПа | 10 | 15 | 20 | 30 | 40 | 50 |
---|---|---|---|---|---|---|
Марка цемента | 300 | 400 | 400 | 600 | 600 | 600 |
В качестве заполнителей бетона стремятся использовать, как правило, местные материалы из близко расположенных карьеров, но отбирают из них те, которые позволяют получать бетон с заданными свойствами при минимальных расходах цемента. Заданную подвижность бетонной смеси обеспечивают правильным назначением расхода воды, а прочность бетона – правильным назначением водоцементного отношения и активности цемента (рис. 6).
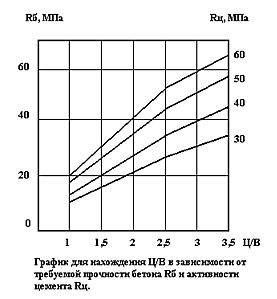
Минимального расхода цемента добиваются правильным выбором содержания крупного и мелкого заполнителя. В современных способах расчета обычно используют коэффициент раздвижки зерен щебня (гравия) раствором, который показывает, насколько объем раствора превышает объем пустот в щебне. В этом случае расходы песка и щебня в тяжелом бетоне определяют по формулам: Щ=1000/( Пщα/ρ’ щ+1/ρщ ); (1) П=ρп(1000-Ц/ρц-В-Щ/ρщ); где (2) Ц, В, П, Щ – соответственно расходы цемента, воды, песка и щебня, кг/м3; ρц, ρп, ρщ – истинные плотности цемента, песка и щебня, кг/л; Пщ – пустотность щебня (относительная величина); α -коэффициент раздвижки зерен щебня раствором; ρ’ щ – плотность щебня, кг/л. Расходы цемента и воды определяются в зависимости от прочности бетона и подвижности смеси, а коэффициент α назначается в соответствии с полученными опытным путем рекомендациями, обеспечивающими наиболее разумное соотношение между песком и щебнем, при котором расход цемента оказывается минимальным.
5.2. Выбор соотношения между мелким и крупным заполнителем.
Одним из основных факторов, определяющих
экономичность состава бетона (по расходу цемента), а также его высокое качество,
является правильный выбор соотношения между мелким и крупным заполнителями r=П/Щ.Оптимальное соотношение r имеет бетонная смесь наибольшей подвижности. Подвижность
бетонной смеси зависит от многих факторов, главным из которых можно считать консистенцию
цементного теста, т.е. соотношение между цементным тестом и заполнителем, между
песком и щебнем (гравием). Минимальной подвижностью при прочих равных условиях
обладает бетонная смесь, в которой цементное тесто лишь заполняет пустоты заполнителя
Для бетонов низких и средних марок, для которых объем цементного теста не превышает
300 л/м3, наиболее пригодна смесь песка и щебня с минимальной
пустотностью. В этом случае достигается наибольшая толщина прослойки цементного
теста и наивысшая подвижность бетонной смеси. В высокопрочных бетонах при высоких
расходах цемента желательно использовать смеси с меньшим содержанием песка. При
определении состава бетона соотношение между песком и щебнем устанавливают с учетом
коэффициента раздвижки α, который для жесткой бетонной смеси при расходе
цемента 200-400 кг/м3равен 1,05-1,15.
Оптимальные значения коэффициента α в пластичной
бетонной смеси зависят от содержания в бетоне цементного теста и крупности песка:
они возрастают с увеличением ЦТ и крупности песка (см. табл. 3).
Таблица 3.
Бетон на мелком песке | Бетон на среднем песке | ||||
---|---|---|---|---|---|
Содержание цементного теста, л/3 | Значенияα | Содержа ние це ментного теста, л/3 | Значенияα | ||
расчетные | действительные | расчетные | действительные | ||
220 | 1,12 | 1,10 | 220 | 1,24 | 1,23 |
280 | 1,32 | 1,28 | 280 | 1,43 | 1,39 |
350 | 1,54 | - | 350 | 1,54 | 1,51 |
Для жестких бетонных смесей при расходе цемента менее 400 кг/м3α следует принимать 1,051,15 (в среднем 1,1). Меньшее значение принимают в случае использования мелких песков. Для пластичных бетонных смесей оптимальные значения α выбирают из таблицы 4:
Таблица 4.
Расход цемента, кг/3 | Оптимальные значения коэффициента α при В/Ц | ||||
---|---|---|---|---|---|
0,4 | 0,5 | 0,6 | 0,7 | 0,8 | |
250 | - | - | 1,26 | 1,32 | 1,38 |
300 | - | 1,30 | 1,36 | 1,42 | - |
350 | 1,32 | 1,38 | 1,44 | - | - |
400 | 1,40 | 1,46 | - | - | - |
500 | 1,50 | 1,56 | - | - | - |
5.3. Порядок расчета состава бетона.
Состав бетонной
смеси выражают двумя способами:
- Соотношением по массе между цементом, песком и гравием (или щебнем) с обязательным указанием водоцементного отношения и активности цемента. Количество цемента принимают за 1, поэтому соотношение между составными частями бетона записывают в виде 1:x:y с указанием В/Ц (например, 1:2:4 по массе при В/Ц=0.6).
- Расходом материалов по массе (кг) на 1 м3 уложенной и уплотненной бетонной смеси, например: цемента – 280; песка – 700; щебня – 1250; воды – 170; итого - 2400.
Порядок расчета
состава бетона следующий:
1. Определяют В/Ц в зависимости от требуемой прочности, срока и условий твердения бетона. В/Ц
находят путем предварительных опытов, устанавливающих зависимость прочности бетона
от этого фактора и активности цемента, или ориентировочно по формулам:
а) Для обычного бетона при В/Ц>0,4 В/Ц=АRц/(Rб+А*0,5Rц);
б) Для высокопрочного бетона при В/Ц<0,4 В/Ц=А1Rц/(Rб-А1*0,5Rц);
Значения коэффициентов А и А1 берут из таблицы 5 либо находят Ц/В по графикам (рис. 6):
Таблица 5.
Материалы для бетона | A | A1 |
---|---|---|
Высококачественные | 0,65 | 0,43 |
Рядовые | 0,60 | 0,40 |
Пониженного качества | 0,55 | 0,37 |
При расчете состава бетона иногда необходимо учитывать
требования к нему по морозостойкости, водонепроницаемости, прочности на растяжение
при изгибе и пр. В этом случае для назначения В/Ц используют соответствующие
зависимости.
2. Определяют
расход воды в зависимости от требуемой подвижности бетонной смеси по графикам
на рис. 8.
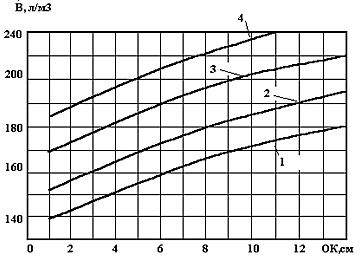
График
водопотребности В пластичной (а) и жесткой (б) бетонной смеси, изготовленной с
применением портландцемента, песка средней крупности (водопотребность 7%) и гравия
наибольшей крупности: 1-70 мм; 2-40 мм; 3-20 мм; 4-10 мм ОК – осадка конуса,
У – удобоукладываемость по техническому визкозиметру Примечания: Если применяют
мелкий песок с водопотребностью свыше 7%, то расход воды увеличивают на 5 л на
каждый процент увеличения водопотребности; при применении крупного песка с водопотребностью
ниже 7% -расход воды уменьшают на 5 л на каждый процент уменьшения водопотребности.
При применении щебня расход воды увеличивают на 10 л. При применении пуццолановых
цементов расход воды увеличивают на 15-20 л. При расходе цемента свыше 400 кг.
Расход воды увеличивают на 10 л на каждые 100 кг увеличения расхода цемента.
3. Определяют
расход цемента: Ц=В:В/Ц. Если расход цемента окажется ниже допустимого по СНиПу
(табл.2), то следует увеличить его до требуемой нормы или ввести тонкомолотую
добавку.
4. Устанавливают
коэффициент раздвижки α для пластичных бетонных смесей по таблице 4.
5. Определяют
расход щебня или гравия по формуле (1).
6. Определяют
расход песка по формуле (2).
7. Проверяют
на пробных замесах подвижность или жесткость бетонной смеси, при необходимости
вносят поправки в расчет состава бетона. Если применяют воздухововлекающие добавки,
то количество вовлеченного воздуха учитывают при подсчете расхода песка.
Определение производственного состава бетона.
На производстве часто применяют при
приготовлении бетона влажные заполнители. Количество влаги, содержащейся в заполнителях,
должно учитываться при определении действительного расхода воды. Вначале определяют
содержание воды в заполнителях по формулам
Вп=ПWп;
Вщ=ПWщ, где Wпи Wщ влажность песка
и щебня (гравия).
Затем устанавливают действительный расход воды:
Вд=В-Вп-Вщ Поскольку часть массы влажных заполнителей составляет
вода, расход песка и щебня увеличивают на массу воды, которая в них содержится:
Пд=П+Вп иЩд=Щ+Вщ Расход цемента
и плотность бетонной смеси при данной корректировке состава остаются неизменными.
5.4. Особенности расчета бетона
с химическими добавками.
Определение состава бетона производят
на основе единой методики, рассмотренной выше, с учетом влияния добавок на основные
зависимости состав-свойство, используемые в расчетах. При этом учитывают, что
добавки не изменяют характера зависимостей подвижности бетонной смеси от расхода
воды и прочности бетона, от активности цемента и цементноводного отношения,
а только изменяют количественное соотношение между разными факторами. Введение
добавок способствует повышению подвижности смеси, уменьшает расход воды, необходимый
для получения равноподвижных смесей, однако основная зависимость ОК=f(В) имеет
одинаковый характер и в обычном бетоне, и в бетоне с добавками. Изменяются только
положение кривой и соответственно получаемые по ней количественные результаты.
Эффект воздействия суперпластификатора на бетонную смесь зависит от количества
введенной добавки и минералогического состава цемента (Таблица 6).
Таблица 6.
Условная группа цемента | Содержание в цементе, % | Среднее уменьшение расхода воды в равноподвижных смесях при дозировке суперпластификатора, % | ||||
---|---|---|---|---|---|---|
C3S | C3A | 0,5 | 0,75 | 1,00 | 1,25 | |
1 | 49 | 6 | 18 | 23 | 28 | 33 |
2 | 40 | 7..8 | 17 | 22 | 27 | 32 |
3 | 33 | 10 | 15 | 19 | 24 | 29 |
Сравнение пластифицирующего действия на бетонную смесь различных суперпластификаторов показало, что оно приблизительно одинаково. Например, при содержании добавки 1% массы цемента и расходе цемента 500 кг/м3снижение водопотребности для разных добавок колебалась от 23 до 25%. Оптимальные дозировки пластифицирующих добавок приведены в Таблице 7, при этом учитывается вид цемента и ожидаемый техникоэкономического эффект: вводится ли эта для повышения подвижности бетонной смеси, либо для сокращения расхода цемента, либо повышения прочности бетона, либо совершенствования формования бетонных и железобетонных изделий.
Таблица 7.
Цемент | Добавки в расчете на сухое вещество, % от массы цемента. | ||
---|---|---|---|
СДБ, УПБ | М, ЛХК | ГРП-1 | |
Портландцемент, быстротвердеющий цемент | 0,15...0,25 | 0,10...0,20 | 0,005...0,01 |
Сульфатостойкий порт ландцемент | 0,10...0,20 | 0,05...0,15 | 0,01...0,02 |
Шлакопортланд-цемент, пуццоланновый цемент | 0,20...0,30 | 0,10...0,20 | 0,01...0,03 |
Приведенные соображения для добавок пластификаторов и суперпластификаторов можно распространить и на случай применения добавокускорителей твердения. Эти добавки, заметно изменяя твердение бетона в раннем возрасте, практически мало влияют на его прочность в возрасте 28 сут. Добавкиускорители твердения должны вводиться в бетонную смесь в оптимальных количествах. Это устанавливается из условия, что добавка оказывает достаточно эффективное воздействие на бетон, но при этом не вызывает побочных отрицательных явлений. При меньшей дозировке добавки падает ее эффективность, при большей - значительно понижается эффект от дополнительного количества добавки, вводимого в бетон сверх оптимального, и, как следствие, могут наступить нежелательные явления например коррозия арматуры).
6. Особенности проектирования состава разных видов тяжелого бетона.
Бетон для сборных железобетонных конструкций.
Для ускорения
твердения бетона при изготовлении сборных ж/б конструкций применяют тепловую обработку.
Рост прочности при этом определяется не только активностью цемента, составом бетона,
консистенцией бетонной смеси, но также режимом тепловой обработки и другими факторами.
В этих условиях наиболее точные результаты можно получить при определении состава
бетона на основе предварительных испытаний. Значение Ц/В для пробных замесов
выбирают по Таблице 8. Указанные пределы Ц/В обеспечивают получение требуемой
отпускной прочности бетона при обычно применяющихся на заводах сборного железобетона
режимах тепловой обработки: предварительная выдержка – 1-2 ч, подъем температуры
– 2-3 ч, изотермическая выдержка – 6-12 ч, остывание – 3-4 ч. Температура изотермической
выдержки для бетона на портландцементе 80°С, для бетона на шлакопортландцементе
90°С.
Таблица 8.
Требуемая прочность бетона R28, МПа | Марка цемента | |||||
---|---|---|---|---|---|---|
300 | 400 | 500 | 600 | |||
Отпускная прочность бетона 70 % R28 | ||||||
10 | 1,0...1,5 | 1,1...1,5 | - | - | ||
15 | 1,2...1,5 | 1,1...1,5 | - | - | ||
20 | 1,5...2,0 | 1,2...2,0 | 1,2...1,5 | - | ||
25 | 1,5...2,2 | 1,2...2,0 | 1,2...1,8 | - | ||
30 | 2,0...2,5 | 1,8...2,2 | 1,5...2,0 | 1,2...1,8 | ||
40 | - | 2,0...2,8 | 2,0...2,4 | 1,5...2,2 | ||
50 | - | - | 2,2...2,8 | 1,8...2,8 | ||
Отпускная прочность бетона 85 % R28 | ||||||
10 | 1,1...2,5 | - | - | - | ||
15 | 1,4...1,8 | 1,2...1,8 | 1,2...1,6 | - | ||
20 | 1,8...2,2 | 1,5...2,0 | 1,4...1,8 | - | ||
30 | - | 2,0...2,5 | 1,8...1,2 | 1,4...2,0 | ||
40 | - | 2,2...2,5 | 2,2...2,5 | 1,8...2,2 | ||
50 | - | - | 2,4...2,8 | 2,2...2,6 |
Если продолжительность режима тепловой обработки задана технологическим регламентом, то по результатам опытов находят зависимости Rотн=f(Ц/В) и R28=f(Ц/В) при заданном режиме и по ним определяют требуемое Ц/В и окончательный состав бетона.
Высокопрочный бетон.
В современных
условиях возможно получать высокопрочные бетоны с прочностью 50-100 МПа и особо
высокопрочные с прочностью более 100
МПа. На практике более широкое применение получили высокопрочные бетоны
с прочностью 50-80 МПа. Для получения высокой прочности необходимо создать особо
плотную, прочную и монолитную структуру бетона. Этого можно достигнуть при выполнении
ряда условий, вытекающих из физических основ структурообразования бетона:
- Применение высокопрочных цементов и заполнителей.
- Предельно низкое водоцементное отношение.
- Высокий предельно допустимый расход цемента.
- Применение суперпластификаторов и комплексных добавок, способствующих получению плотной структуры бетона.
- Особо тщательное перемешивание и уплотнение бетонной смеси.
- Создание наиболее благоприятных условий твердения бетона. Для высокопрочных бетонов следует принять цементы активностью выше 50 МПа желательно с низкими значениями нормальной густоты. Заполнители должны быть чистыми и обладать хорошим зерновым составом и малой пустотностью, не содержать по возможности слабых зерен. Предел прочности крупного заполнителя должен быть на 20 % выше заданной прочности бетона. Для особо высокопрочных бетонов применяют заполнители повышенной прочности из диабаза и базальта. Высокая плотность и прочность бетона достигаются применением предельно низкого водоцементного отношения (<0,4), что требует использования специальных приемов, позволяющих плотно укладывать бетонные смеси в этом случае. К таким приемам относится применение суперпластификаторов или комплексных добавок, содержащих повышенную дозу пластификатора, ускорителя твердения и антивовлекающий компонент, либо использование особо интенсивных способов уплотнения бетонной смеси (прессование или роликовый прокат). Наилучшими условиями для твердения высокопрочного бетона являются нормальные (температура 20-25°С, влажность 100%). С повышением температуры и особенно при тепловой обработке в твердеющем бетоне возникают градиенты температуры и влажности, приводящие к миграции влаги, к температурновлажностным деформациям и неравномерной усадке цементного камня.
Быстротвердеющий бетон.
Получение быстротвердеющего бетона,
обладающего относительно высокой прочностью в раннем возрасте (1-3 сут.) при твердении
в нормальных условиях, достигается применением быстротвердеющего цемента, а также
различными способами ускорения твердения цемента.
К этим способам относятся:
- Применение жесткой бетонной смеси с низкими значениями В/Ц отношения.
- Использование добавок – ускорителей твердения (хлористый кальций), глиноземистого цемента и др.
- Сухое или мокрое домалывание цемента с добавкой гипса (2-5 % от массы цемента).
- Активация цементного раствора. При выборе состава бетона можно пользоваться данными табл. 9, где показана зависимость между прочностью бетона в раннем возрасте и различными способами ускорения твердения бетона.
Таблица 9.
Способ ускорения твердения | Повышение предела прочности бетона при сжатии по сравнению с обычным бетоном на цементе М400-500, % в возрасте | |
---|---|---|
1 сут. | 2 сут. | |
Применение БТЦ или цемента М600 | 130...170 | 115...135 |
Добавка 2% хлористого кальция от массы цемента | 150...200 | 125...150 |
Дополнительный помол цемента с добавкой 2-3% гипса до удельной поверхности 5000-6000 см2/г |
200...250 | 150...200 |
Активация бетонной смеси или цемента, виброперемешивание |
140...170 | 120...300 |
Дополнительный помол цемента, добавка 2% CaCl2 и активация бетонной смеси (совместное действие) |
300...400 | 200...300 |
Экспериментальная проверка и корректировка по ее результатам состава быстротвердеющего бетона обязательны, так как увеличение прочности бетона в раннем возрасте в результате применения того или иного способа ускорения твердения в значительной степени зависит от вида цемента, состава бетона и других факторов, а также увеличение прочности бетона при применении нескольких способов не является прямой суммой значений прироста прочности бетона, достигаемого каждым способом в отдельности.
Бетон для гидротехнических
сооружений.
Бетон
для гидротехнических сооружений должен обеспечивать длительную службу конструкций,
постоянно или периодически омываемых водой. Поэтому
к нему помимо требований прочности предъявляются также требования по водонепроницаемости,
а нередко и по морозостойкости. Состав гидротехнического бетона можно определить
рассмотренным выше методом. Специальные свойства этого бетона, например, водонепроницаемость
обеспечиваются:
- выбором материалов, обеспечивающих требуемые морозостойкость и водонепроницаемость;
- определением В/Ц не только из уровня прочности, но и из условия долговечности;
- назначением расхода цемента в определенных пределах;
- выбором коэффициента раздвижки, обеспечивающего получение плотного и долговечного бетона;
- применение микронаполнителей, уменьшающих тепловыделение и объемные деформации и гарантирующих получение плотного бетона при низких расходах цемента;
- применение воздухововлекающих добавок. Для гидротехнического бетона допускается применение портландцемента, пластифицированного и гидрофобного цементов, пуццоланового и шлакового, а в некоторых случаях сульфатостойкого цемента. Для повышения водонепроницаемости и морозостойкости бетона применяют химические добавки (СДБ, СНВ). Для уменьшения расхода цемента, а, следовательно, тепловыделения и объемных деформаций бетона при сохранении необходимой подвижности бетонной смеси и плотности бетона в него вводят различные микронаполнители (золу-унос). В таблице 10 представлены физикомеханические характеристики бетона для гидротехнических сооружений.
Таблица 10.
Конструкция | Удобо- укладыва- емость, с |
Осадка конуса бетонной смеси, см | ||||
---|---|---|---|---|---|---|
На строительном песке | На мелкозернистом песке | |||||
Без добавки | С добавкой | Без добавки | С добавкой | |||
Массивные бетонные и малоармированные с содержанием арматуры до 0,5% | 5...8 | 2...4 | 1...3 | 1...3 | 1...2 | |
Железобетонные с содержанием арматуры до 1% | 3...5 | 4...8 | 3..6 | 3...6 | 2...5 | |
То же, более 1% | 2...3 | 8...14 | 6...10 | 6...10 | 5...8 |
Расход цемента должен быть больше минимальных значений, обеспечивающих получение плотного бетона, и в тоже время по условиям тепловыделения его не должно быть для массивных конструкций более 350 кг/м3, а немассивных – 400 кг/м3. Для получения водонепроницаемости бетона содержание песка в смеси заполнителей должно быть несколько увеличено против обычных значений. В связи с этим коэффициент раздвижки надо принимать на 0,03-0,06 больше, чем указано в таблице 4. Оптимальное значение также определяют опытным путем из условия получения наиболее плотной бетонной смеси.
Бетон для дорожных и аэродромных
покрытий.
В бетонных
покрытиях дорог и азродромов основными расчетными напряжениями являются напряжения
от изгиба, так как покрытие работает на изгиб, как плита на упругом основании.
Поэтому
при расчете состава бетона надо установить такое соотношение между его составляющими,
которое обеспечивает требуемую прочность бетона на растяжение при изгибе, а также
достаточную прочность на сжатие и морозостойкость. Проектную прочность дорожного
бетона устанавливают в зависимости от назначения бетона (Таблица 11).
Таблица 11.
Назначение бетона | Заданная прочность, МПА | ||
---|---|---|---|
При изгибе | При сжатии | ||
Для однослойных и верхнего слоя двухслойных покрытий | 4,0;5,5;5,0;5,5 | 30, 35, 40, 50 | |
Для нижнего слоя двухслойных покрытий | 3,5; 4,0; 4,5 | 25, 30, 35 | |
Для оснований усовершенствованных капитальных покрытий | 2,0;2,5;3,0;3,5 | 10, 15, 20, 25 |
Для обеспечения требуемой морозостойкости бетона и его стойкости против совместного действия хлористых солей, применяемых для борьбы с гололедом, и замораживания бетона при отрицательных температурах В/Ц следует принимать для однослойных и верхнего слоя двухслойных покрытий не более 0,5, для нижнего слоя двухслойных покрытий – не более 0,6, для оснований усовершенствованных покрытий – не более 0,75. Для качественного уплотнения бетонная смесь должна иметь показатели подвижности или жесткости, приведенные в таблице 12, определяемые непосредственно перед укладкой в покрытие или основание.
Таблица 12.
Уплотнение бетонной смеси | Осадка конуса, см | Жесткость, с |
---|---|---|
Уплотнение покрытий бетоноукладочными машинами | 1...2 | 2...5 |
Уплотнение покрытий площадочными вибраторами | 2...3 | - |
Уплотнение оснований | - | 10...15 |
Бетонные смеси с небольшим избытком песка, хотя и имеют несколько повышенную жесткость, но хорошо укладываются в покрытие, сохраняют прочность при изгибе, не расслаиваются и дают при этом лучшее качество поверхности. При этом коэффициент раздвижки зерен заполнителя можно назначать 1,3-1,7, для жестких смесей – 1,25-1,3. С каждым годом возрастает разнообразие бетонов, вяжущих веществ, заполнителей, технологических приемов производства сборного и монолитного железобетона, применяемых в строительстве. Поэтому мы рассмотрели самые основные виды бетонов, вяжущих веществ, заполнителей, добавок. Большое внимание было уделено требованиям к компонентам бетонной смеси, взаимосвязи между качеством составляющих бетонной смеси и качеством бетона. Также были рассмотрены основные концепции расчета бетонной смеси, особенности такого расчета для основных видов бетона.
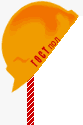

© ООО «ГОСТпол»
тел. +7 (495) 210-32-51, 210-62-09
info@gostpol.ru http://gostpol.ru
дизайн и разработка printstudio.ru